Following are my Major
Accomplishments working in the Manufacturing Industry, in various positions from
my early introduction as Assistant Foreman through Foreman, Production Manager,
Plant Manager, Buyer, Purchasing Manager, Manufacturing Manager, Vice President
and finally as Manufacturing Consultant.
WHITTET-HIGGINS CO., CENTRAL FALLS, R.I.
Within my first month with this organization through competitive bidding,
I reduced the cost
of cutting and lubricating oils from $3.35 per gallon
to $2.05 per gallon. this resulted in a cost savings
of $10,400 per year
.
With the use of my home computer and
Lotus software set up a number of programs and weekly
reports which quickly gave instant information on operator
efficiency to time standards in the screw machine department
and secondary machining department.
Completely setup a new product line with
the help of a manufacturing Engineer. This included design
of product and tooling, The supervision of tool
manufacturing, and initial production setups and runs. The
establishment of computer reports on costs. The control of
outside machine builders of specialized machines.
Reduced the use of trichloroethylene from
over 10,000 pounds per year to less than 5,000 pounds. This
was accomplished by using water soluble cleaners in process
and containing the hazardous liquids in such a way to
prevent evaporation to the environment.
Introduced SPC to the factory through the use of
electronic data collection devices in conjunction with computer programming. Trained all personnel in its use and
value.
Conducted weekly training
courses for personnel in decimals, fractions, algebra
trigonometry, Machining Fundamentals, solving machining problems.
Tooling Technology.
Wrote and instituted all OSHA Safety Procedures as required by
OSHA. Wrote and instituted all Hazardous Chemicals and waste
procedures, as required by the U.S. and State
Government.
Instrumental in the justification, purchase negotiation,
purchase contract development of Capitol
Equipment.
Introduced new methods of manufacturing which produced a
better quality product at less cost.
BULOVA CORPORATE PURCHASING
Devised and instituted a standard
purchasing form for complete watch on site purchasing. This
for the first time in the history of the Bulova Watch
Company, made it possible for Bulova purchase orders to be a
complete contract. Containing articles for cost breakdowns
required by customs, free spare watch quantities, complete
delivery schedules, complete shipping instructions, Gold
values date of order, order confirmation, specifications of
manufacture, acceptance and inspection criteria, drawings,
freight forwarders, progress reporting, invoicing
procedures, warranty and in warranty repair clause, product
information clause, exclusivity clause, spare parts
availability, insurance, and reorder maximum pricing clause.
Devised and instituted procedures for
establishing manufacturing estimates for product to be
purchased, prior to on site purchase. This provided a window
of purchase price between the manufacturing cost estimate
and the calculated maximum purchase price as set by the
marketing selling price. Again a first for Bulova, it
prevented a multitude of problems encountered in the field.
During product reordering trips, which
occurred two to four times a year. I was always able
to negotiate a lower price with a cost savings of $200,000
to $600,000 per reordering trip cycle.
Devised and instituted a procedure for new vendor
evaluation. Upon completion of a new facility visit and completion of the
procedural
report, a committee would meet and approve or disapprove
the vendor
from information provided in my report.
Sat on the business planning committee for the
development of plans to increase the companies market share in the industry.
BULOVA WATCH CASE MANUFACTURING
Changed many old established methods of manufacturing
watch cases to more efficient methods, with the results of reducing the
average watchcase manufacturing time from twenty five minutes to
fifteen minutes.
Instituted simple production control methods, prepared
and maintained by the individual department supervisor. This yielded
invaluable information as to product location in the manufacturing
process. Instituted simple quality control records which provided
historical data on product processed.
When it became necessary for the watchcase division to
provide a watchcase and an attachment, I was assigned the total
responsibility of making this a reality. I set up purchasing procedures,
located sources worldwide, source inspected, negotiated contracts
on site, controlled quality and delivery to coincide with
manufacturing.
Due my efforts in this responsibility, the addition of
attachments to the watchcase division was a total success.
BULOVA INDUSTRIAL DIVISION
With a team of four people, one mechanical engineer, one
manufacturing engineer (myself), and two toolmakers we developed, built
and debugged a hydraulic, pneumatic, mechanical manufacturing machine,
which at that time was an innovation to the industry. The machine was
considered one of the first mechanical robots.
With one operator who
loaded and placed a fixture on a track, the machine performed 250 different
machining operations in seven seconds. Furthermore, within this time
period the part was unloaded, the fixture cleaned, automatic fixture
return to the operator and the part checked for broken tools.
In the fuze (Motor Shell contact fuze) department we manufactured two million fuzes
for the U.S.
Government without one failure. I believe this type of
performance can only be accomplished with happy and contented
employees. I always motivated and insisted on very close employee
relations.
GRIES REPRODUCERS, WARREN, R.I.
Motivated the company to change from standard paint
spraying to electro-static spraying on the product. This change reduced rejects
from 10% to less than 1%. Reduced paint consumption by 30% and cut
paint line maintenance in half.
GENERAL PRECISION LABORATORIES, DIVISION OF SINGER
As manager of fabrication, I was the main instrument in
the motivation of employees in fabrication to change from a cost plus
operation to a non-incentive piece rate system. This included
introduction of operation sheets with accurate time studies for each
operation.
I feel that this change in manufacturing was highly instrumental
in making the company successful on future government contract
bidding.
Motivated and worked with sixty five machine and sheet
metal shop employees to participate in a zero defects program,
consequently, for four straight months we had no defects. ( I hold a
letter of commendation reflecting this.)
Submitted many cost reductions which were mainly due to
the institution of the non-incentive piece rate system and changes made to more efficient methods. (I hold a letter of
commendation reflecting this.)
I have been a Hands On Person no mater
what position or title I have held. This experience makes me a
valuable source of information for any type of Manufacturing Environment.
I am available for any inquiry you may
have, I will listen to all your suggestions and accommodate to your needs and
unique environment. I am sure my extensive background in all Manufacturing aspects
will be of significant value to you. Contact me through my address,
phone, e-mail or fax as you wish.
MARSCHALL MANUFACTURING CONSULTANT
SERVICES
71 HOPKINS AVE.
JOHNSTON, RHODE ISLAND 02919
401-934-2764
E-MAIL: CLICK ON ICON, 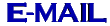